World's Most Dynamic
Turbines Engines Hydraulic Motors Compressors Pumps
Technical
Pistons & Cranks Are Poor Expanders

The illustration above highlights the benefits of the Vengeance Vane & Rotor expander design over the traditional piston & crank design. For simplicity, a piston expander with a 1:1 bore-to-stroke ratio (bore diameter = vertical stroke length) is used as a benchmark. Modern piston engines/expanders may vary slightly from this ratio but can never come close to the incredible torque of the Vengeance design with the same pressure input.
Compare the forces acting on the Piston and on the Vanes under equal pressure. Much more force acts on the piston and crank components but provides much less torque. This is a major flaw in the piston & crank expander design and a tremendous waste of energy.
The Vengeance engine size depicted above is less than half the size of an equal displacement V-8 Piston 4-stroke internal combustion engine and smaller than an equal displacement 4-cylinder 2-stroke engine or expander. Other Vengeance designs can deliver more than double the torque.
Multistage Piston Expanders – Drawbacks
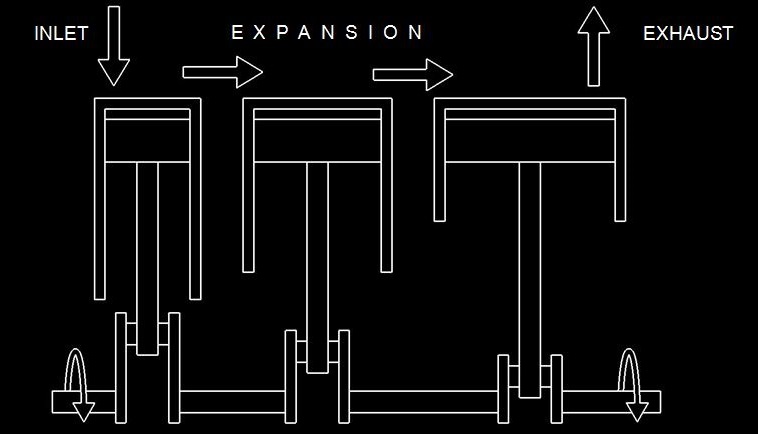
For a single piston expander, very long expansion strokes are too impractical. Conventional piston expanders require multiple stages for efficiency. Just like the traditional turbine example, as the gas expands, the pressure drops requiring more sets of larger and larger pistons. Again, this drastically increases the complexity, cost, size, weight and part count.
More Advantages Over Pistons
- High power-to-weight ratio
- Less friction
- Low operating and maintenance costs
- Low part count
- Low manufacturing costs
- Low noise & vibration
- Higher efficiency
- Multi-fuel capability
- Does not require oil for lubrication
Advantages Over Conventional Steam Turbines

Conventional Rankine cycle/steam turbines are designed to run at maximum efficiency at speeds so high that any condensate droplets forming downstream in the exhaust section can lead to erosion and catastrophic damage to the blades and bearings. For this reason, more heat is added to ensure the vapor remains above 90% dryness. Some turbines add more than one re-heat stage to keep the steam within the Dry Saturated Vapor region. The extra heat and equipment added for superheating comes with a heavy price tag. Furthermore, in a closed-loop system, any residual superheat will have to be dealt with in the condenser. This also increases the size, cost and loading of the condensing unit.
The Vengeance Expander design allows more expansion, going deeper into the wet vapor region as it can tolerate high condensate formation. In fact, the Vengeance design can operate as an excellent hydraulic motor or pump. Allowing more expansion decreases exhaust pressure and temperature, putting less strain on the condensers and increases net system efficiency. It also allows for more efficient use of low heat and low pressure “wet steam” boilers and pressurized refrigerant-driven Organic Rankine Cycle (ORC) heat exchanger/evaporator systems.
More Advantages Over Turbines
- Comparatively high electric efficiency for small-scale CHP units up to 2 MW
- Excellent partial-load efficiency over a wide range of load conditions
- Runs efficiently in both back-pressure and condensing turbine modes
- Load fluctuations between 10% and 100% duty cycle are no problem
- Not sensitive to steam quality or flow fluctuations
- No high velocity steam nozzles to clog or clean periodically
- Rapid stop and start times
- Water droplets in steam supply pose no threat
- Simple throttle control for less complex automation requirements
- Compact size, rugged construction, easy setup, low operating & maintenance costs
- No need for isolated anti-vibration concrete pad
- Lower speeds increase component durability and life cycle (seals, bearings, etc.)
- Does not require oil for lubrication