World's Most Dynamic
Turbines Engines Hydraulic Motors Compressors Pumps
Real Progress Through Continuous Research and Development
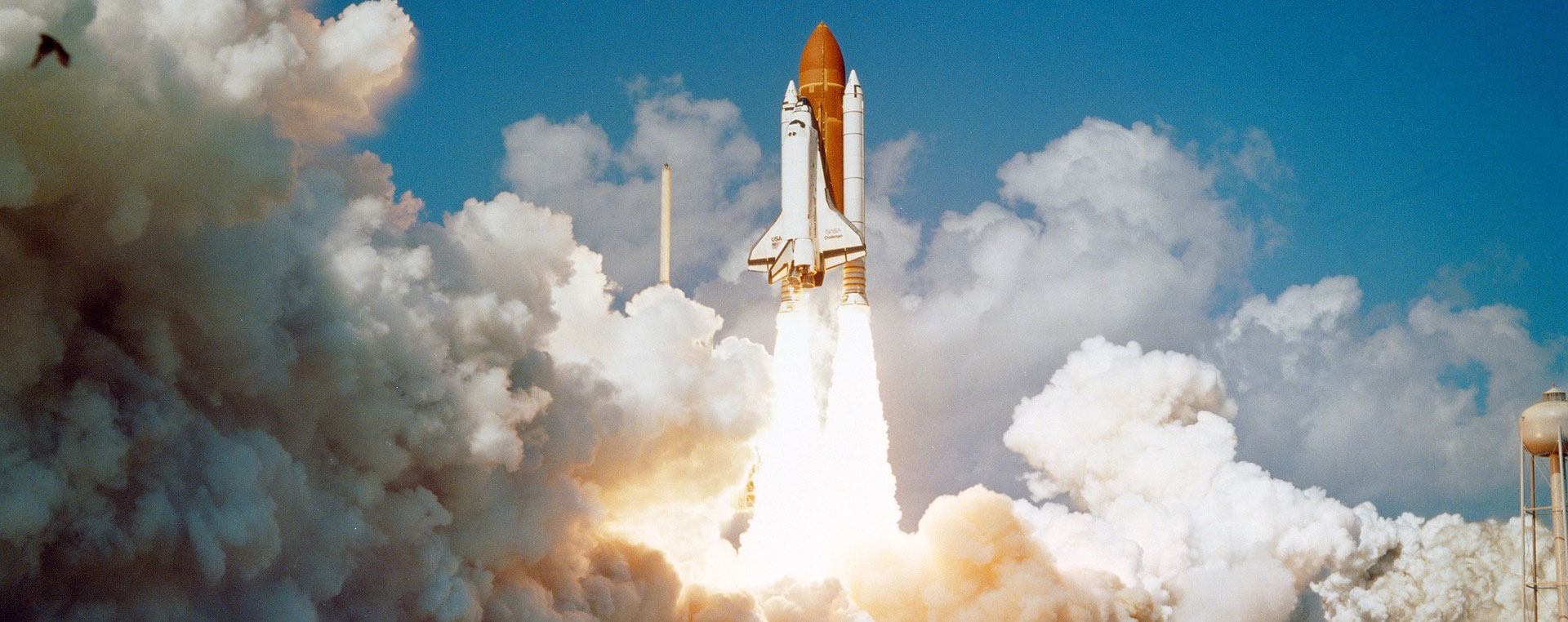
Recent Developments
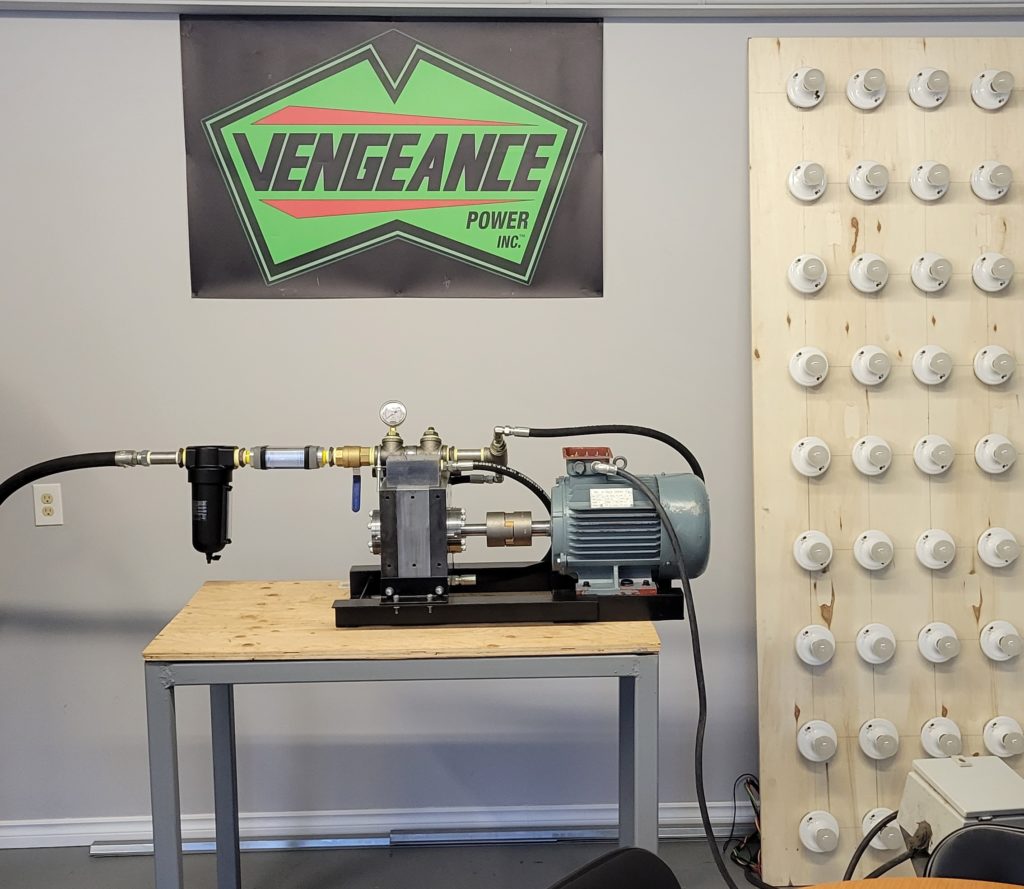
[Click image to see video]
First run test of our new dry internal seal and bearing design Expander Motors.
Dry seals and bearings have the benefit of oil-free operation in extreme heat or cold conditions where oil lubricant would fail. Another benefit is no need to separate lubricant oil from the working fluid. This is beneficial when using Steam or other fluids such as ORC refrigerants that do not work well with oil.
Seen here is a small production-ready model running on a tank of compressed air. We charged up the tank and shut off the compressor. The stored air drives the Expander as the pressure drops. This is ideal for pressure-letdown applications such as with Natural Gas. As you can see, our Expander has the torque to drive this load immediately from a dead stop with no problem. It is connected to a low rpm synchronous 3-Phase AC permanent magnet generator with a direct 1:1 speed coupling. The live load consists of 36 x 100-watt real incandescent bulbs, not LEDs.
Now offering our newest Expander Genset combinations, custom designed and built for your application
Prices start as Low as $650 USD / KW
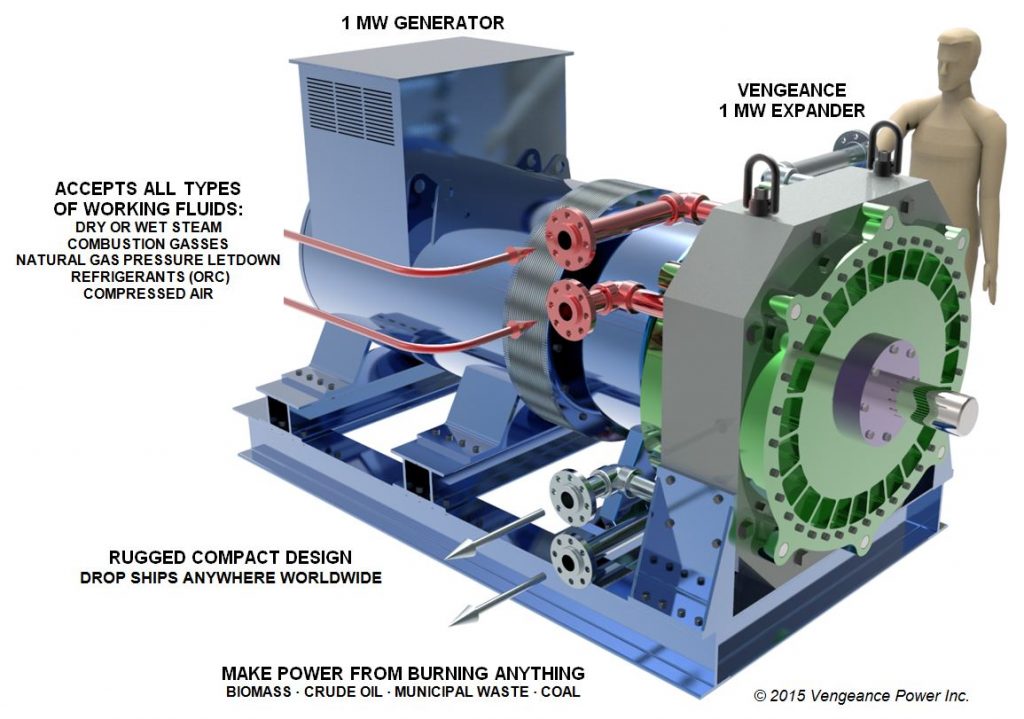
Our Genset units can be powered by any fluid at any pressure and temperature delivering:
- Robust, durable, on-demand high torque performance
- Lower up-front, operating & maintenance costs, shorter delivery times, faster return on investment
- Easy throttling for optimal power output with varying pressures
Choose your driving fluid:
- Wet/Dry Steam
- Combustion Gasses
- Natural Gas Pressure Letdown (NGPL)
- Compressed Air for Compressed Air Energy Storage & Power (CAESP) applications
- ORC Fluid/Refrigerants (R245FA, R410A, R744, R290, R601A, R728…)
- Other fluids (Benzene, Toluene, Cyclopentane, Propane, Ammonia, Ammonia/Water for Kalina Cycle)
- Supercritical fluids such as CO2
- Hydraulic fluid – Yes, it can also run as a tremendously powerful hydraulic motor!
Choose Your Generator
- We also offer custom designed frame mounted Generator kits
- Rugged welded steel frame for lifting and transport
- Use your own engines – give us your specs and we will make it fit
- 50Hz / 60Hz, 3-phase / 1-phase, AC / DC, 200-600Volt
- Alternator, self-starter, standalone multi-pole PMG types
- 5, 10, 20, 50, 100, 250, 500, 1000kW output
- 300 – 3600 RPM
- Make Power Now!!
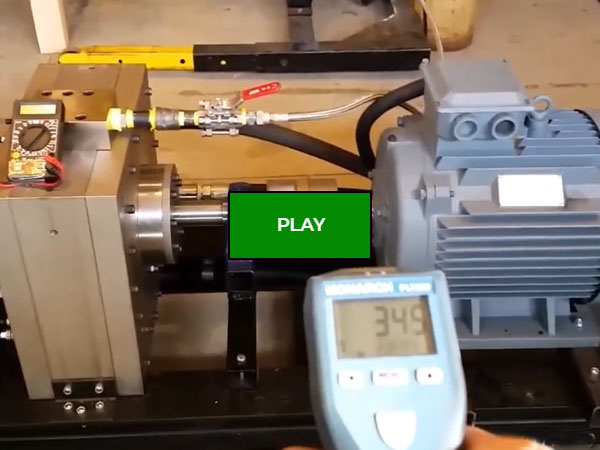
[Click image to see video]
Our latest 20kW class Expander/Genset unit seen here spooling up on compressed air. Voltmeter is attached to phase 1-2 power leads showing AC volts. Shaft speed is measured by a hand-held laser RPM meter and reflective tape on the shaft coupler. Shown here is a multi-pole Permanent Magnet Generator, self-powered, 240V AC 3Phase 50Hz 500RPM with over 90% electrical efficiency. We have plenty of torque for low speed power with a simple, direct 1:1 drive speed coupler. No more annoying gearboxes!
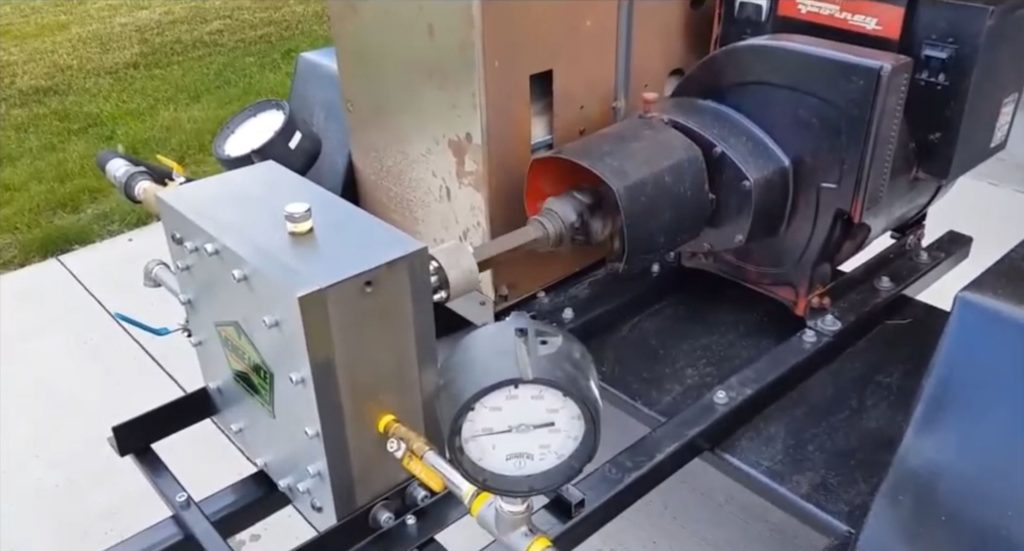
This test demonstrated one of our latest designs for taking low pressure and producing high torque in the most efficient and inexpensive way. The engine was operated on compressed air at only 125 psig without a muffler or electronic controls. This new design is capable of accepting pressures in excess of 3000 psig and temperatures exceeding 500 Deg.C. It can also handle cryogenic conditions. Power output range and size can easily be scaled to any requirement. Moisture condensing inside the engine is no problem for the materials or the cycle at any speed. High torque and low RPM translates into greater reliability and lower manufacturing and maintenance costs. With fewer simple moving parts, the costs of manufacturing and ownership are unmatched by any competitor in the industry with simple, cheap and fast overhauls on-site.
The Engine can run with any type of working fluid without the requirement of oil including:
- Hot gasses for combustion applications
- Dry or Wet Steam for Rankine Cycle applications
- Compressed gasses such as natural gas for pressure letdown (NGPL) applications
- Air for CAESP (Compressed Air Energy Storage & Power) applications
- Hydraulic fluid for heavy industrial applications
- ORC fluids such as natural and synthetic refrigerants for WHR (Waste Heat Recovery) applications
- Supercritical single-state fluids and Stirling Cycles eliminating the need for condensers
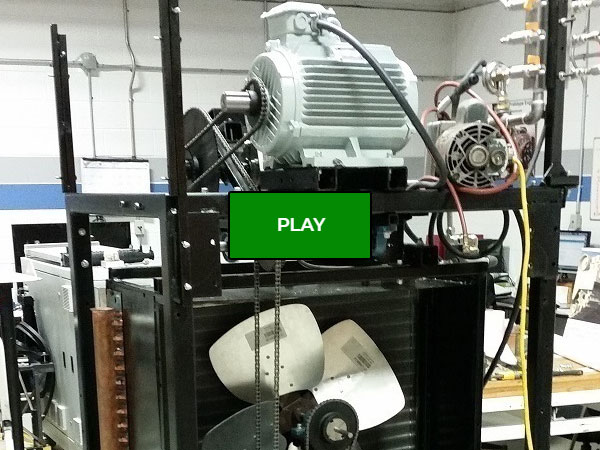
[Click image to see video]
Our first prototype Waste Heat Recovery Organic Rankine Cycle (ORC) system test just before the winter Holiday season. We wrapped some short lengths of tubing around the exhaust ducts of a factory that uses ovens for baked-on paint finishes of steel parts.
This is the least ideal and most crude form of heat extraction but it is completely non-intrusive to the factory equipment. We can run the system with absolutely no adverse effects on the factory process. We can also fully integrate the system to access all of the waste heat for maximum efficiency if desired.
Using a low boiling point, non toxic, non ozone depleting, non flammable ORC fluid (R245FA), we ran a 3-phase AC permanent magnet generator and made some power. As you can see in the video, it easily powered six 100-watt light bulbs and all the mechanical drive gear with less than 100 psig system pressure.
This system configuration using the full exhaust heat flow could generate up to 50 kW using a larger generator.
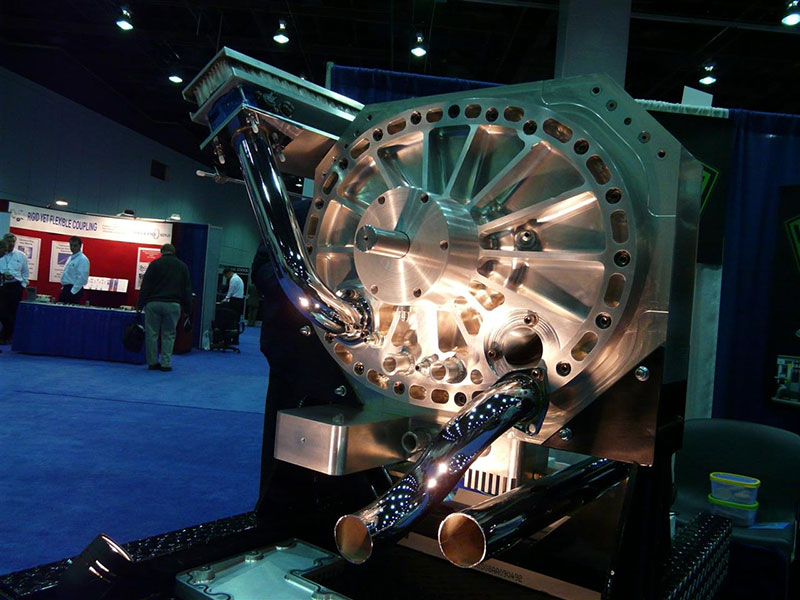
The Power of Leverage
The Vengeance Power Turbine is a unique torque-multiplying positive displacement sealed turbine and a true rotary engine. It is a true rotary because it does not use a crankshaft to transfer reciprocating motion into rotary motion, which reduces the efficiency of the engine. The forces from the expanding gasses from combustion, steam, compressed air or any other working fluid are transferred directly into rotary motion, simplifying the process and converting more of the energy into mechanical work.
Since our turbine is of a positive displacement type, it can easily be throttled for various RPM. It provides maximum torque at start-up/stall. It can also idle and run at very low RPM without stalling like traditional turbines. It also does not require high velocities to compensate for blow-by past the vane tips like traditional turbines. The exhaust temperatures are much cooler since more of the thermal expansion energy is transferred into mechanical energy to turn the output shaft. Our simple design allows the engine to be scaled to any size for any power requirement.
Our turbines use many off-the-shelf components that have gone through rigorous testing under very harsh conditions before implementation. Since our turbines can run at lower speeds with optimal power delivery, reliability is greatly increased.
As an internal combustion turbine engine, it can burn conventional fuels such as: gasoline, diesel, natural gas, propane and alternative fuels such as bio-diesel, ethanol, methanol, syngas and dimethyl ether. Zero carbon fuels such as hydrogen, ammonia, hydrazine, etc.
As an external combustion turbine engine, it can operate on the Brayton Cycle to cleanly and optimally burn a great variety of fuels. Future applications of our technology include hypersonic pulse detonation waves that would destroy most traditional turbine engines.
Past Developments
Click here to see video demonstration of our engine running on the Otto Cycle using our chassis dyno platform.
Click here to see video demonstration (Vengeance Power Engine External Combustion Unit Test)
Click here to see video demonstration of our Vengeance Power Engine running on steam using the Rankine Cycle.
Click here to see video demonstration of our Vengeance Power Engine running on compressed air followed by a lever arm torque test.
Click here to see video demonstration of our Vengeance Power Expander powering a 1972 Corvette Chassis running on compressed air.
Click here to see video demonstration of our Vengeance Power Expander Motor in a 1972 Corvette Chassis.
Click here to see video demonstration of our Vengeance Power Expander in a 1972 Corvette Chassis – Compressed air test running 23 ACFM @ 90 psig.